How an ancient Roman cement recipe could help reduce global warming
New study brings scientists closer to creating concrete that rivals blend used in Rome 2,000 years ago
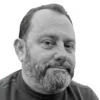
Writing in 79 CE, the Roman scholar Pliny the Elder described underwater concrete structures built by his compatriots that become “a single stone mass, impregnable to the waves and every day stronger.”
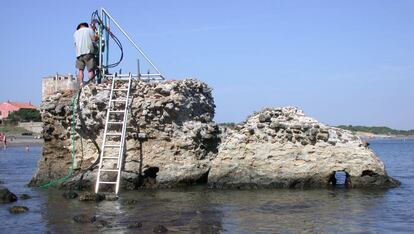
For centuries, Rome built its harbors with a combination of caementum, quicklime and volcanic materials that modern engineering has spent centuries trying to equal. Now, geologists and engineers are examining the remains of Roman ports to find the exact formula needed for the concrete of the future.
Modern concrete begins to deteriorate when it comes into contact with the sea. Its interaction with salt water causes it to lose alkalinity and undergo carbonation, which weakens its surrounding protective layer. Yet astoundingly, despite the passage of so much time, docks that were built by Roman engineers some 2,000 years ago still stand.
The Romans created a concrete that improved with chemical exchange from seawater
Marie Jackson, geologist at the University of Utah
“Contrary to the foundations of modern concrete, based on cement, the Romans created a concrete that improved with open chemical exchange from seawater,” explains Marie Jackson, a geologist at the University of Utah who has spent years searching for the formula of Roman concrete. Both then and now, an agglomerate – or hardening agent – was used. Today, the most common base of concrete is called Portland cement, composed of limestone and clay, heated to more than 1,500°C. Conversely, the Romans relied on a particular type of quicklime: calcium oxide. Today, we use gravels and sands as an aggregate. Back then, any kind of rubble was employed.
But the secret is in the mix. Before the Romans, construction in the most advanced civilizations, like ancient Greece, employed a chalky mortar that agglomerated when it dried. Whether by chance, geographic proximity, or trial and error, it was eventually discovered that the volcanic materials used were reacting with water, as Portland cement does today. In fact, as Pliny wrote, that cement was improved through exposure to seawater.

State of the art technology has enabled Jackson and her colleagues to learn more about these materials. Under an electron microscope at Lawrence Berkeley National Laboratory, a sample from a Roman harbor built between the first and second centuries CE revealed its secrets.
“We could identify different minerals and the complex, enigmatic crystallization sequences at the microscopic level,” says Jackson. According to the results of her investigation, published in the journal American Mineralogist, the limestone, when exposed to seawater, rapidly reacted with the volcanic ash. But what they have also confirmed is that, after the limestone has been used up, a second, much slower, phase begins.
During this second chemical reaction, two minerals – neither of which were properly understood in Roman times – play a key role: tobermorite and phillipsite. In the concrete employed at Roman harbors, these minerals formed thin fibers and plaques that made them more resistant and less susceptible to breaking.
If Roman concrete could be recreated, global warming would be reduced
Both tobermorite and phillipsite are still used today in the production of special cements, but the problem with using them regularly is that they must be heated to a very high temperature, an issue that seems to have been avoided in antiquity. “No one has created tobermorite at 20°C, except the Romans,” explains Jackson.
Víctor Yepes, professor of construction engineering at the Polytechnic University of Valencia, is slightly more measured in his admiration: “Roman concrete was better than bad concrete from the present day, but it was not better than good concrete.” Still, he marvels at the fact that the Romans found materials in nature that modern science took centuries to reproduce with the discovery of Portland cement.
Yepes also acknowledges the great innovation of Roman engineers in the use of pozzolanic materials – i.e., those naturally occurring from volcanic rock – “a use that did not generate CO2 emissions in its production, a stark difference from today.” The cement industry is responsible for 5% of CO2 emissions, which are the cause of climate change.
If the cold reaction of Roman marine concrete could be recreated, the cement manufacturing industry’s contribution to global warming would be dramatically reduced. This is the goal that Jackson, alongside others, including the US Department of Energy, are working toward. Although they have produced experiments in similar conditions, using water from the San Francisco Bay and volcanic materials from the west of the United States, the concrete they obtained does not possess the essential Roman characteristics. While the once secret ingredients have now been disclosed thanks to modern technology, Jackson acknowledges that they still have yet to determine the “preparation of the raw materials and the processing.”
English version by Henry Hahn
Tu suscripción se está usando en otro dispositivo
¿Quieres añadir otro usuario a tu suscripción?
Si continúas leyendo en este dispositivo, no se podrá leer en el otro.
FlechaTu suscripción se está usando en otro dispositivo y solo puedes acceder a EL PAÍS desde un dispositivo a la vez.
Si quieres compartir tu cuenta, cambia tu suscripción a la modalidad Premium, así podrás añadir otro usuario. Cada uno accederá con su propia cuenta de email, lo que os permitirá personalizar vuestra experiencia en EL PAÍS.
¿Tienes una suscripción de empresa? Accede aquí para contratar más cuentas.
En el caso de no saber quién está usando tu cuenta, te recomendamos cambiar tu contraseña aquí.
Si decides continuar compartiendo tu cuenta, este mensaje se mostrará en tu dispositivo y en el de la otra persona que está usando tu cuenta de forma indefinida, afectando a tu experiencia de lectura. Puedes consultar aquí los términos y condiciones de la suscripción digital.