The waning charm of China: Multinationals seek alternatives to produce goods in Asia
The clash between Beijing and Washington, the rise in Chinese wages and the fallout from strict Covid lockdowns prompts companies to diversify production in countries such as Vietnam, Thailand and India
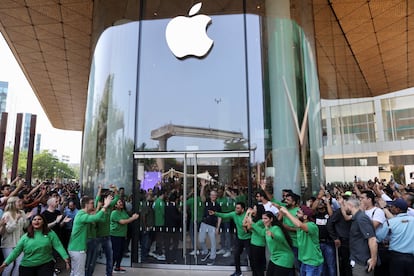
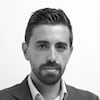
Globalization was for a long time just a matter of price. It was about finding the cheapest goods or the places where it cost the least to produce them, and then getting them to consumers to extract the greatest possible profit margin. That goal is still part of its essence, but since the outbreak of the Covid-19 pandemic and the war in Ukraine, another factor has gained ground in the companies’ strategy: security of supply.
It is useless to produce cheaply if restrictive laws keep factories closed beyond what seems reasonable, as China did when the coronavirus spread. Nor does it make sense to invest in a state that attacks its neighbor and attracts international sanctions, as is the case with Russia. Or to bet on a nation embargoed for production of high-tech chips for fear it will use them for military purposes against nearby Taiwan, i.e. China once again.
The Asian giant, once considered the place to be, is now viewed with suspicion by multinationals. The idea is that you still have to be there, because it is a market of more than 1.4 billion people with decades of accumulated industrial knowledge, which earned it the nickname of the world’s factory. But its appeal is diminishing as the risks grow: wages have risen as its economy has developed, making it less competitive; the geopolitical question of its clash with the United States comes and goes, and any miscalculation in that balance would prove fatal; meanwhile the extremely strict lockdowns imposed by Beijing in its zero-covid policy, which left drivers and other key workers at home, and some large ports and factories running at low speed, showcased the dangers of putting all your eggs in the same basket and underscored the need to diversify.
At a time when there are crises in the supply chains — from the recent lack of vegetables in the United Kingdom to the traffic jam in the Panama Canal due to lack of water, or the drought that has caused shortages of agricultural products in different parts of the world — and where environmental issues have become more important, extending the debate on whether it is really necessary for certain products to travel thousands of kilometers to reach the customer, companies are embarking on a double process: looking for suppliers closer to home, even at the cost of paying them more, and supplementing their exposure to China to reduce uncertainty. This movement has been dubbed China Plus One. This does not imply a massive exit from China — “there are ups and downs, but China is still by far the largest manufacturing market in the world. It will not collapse,” said a senior manager of the Danish shipping company Maersk at the beginning of the year — but companies are branching out to other areas.
“The countries that are benefiting the most are Vietnam, Thailand, Mexico and Turkey,” says Carlos Cordón, professor of Supply Chain Strategy and Management at the Swiss business school IMD. “Apple, for example, is being supplied, in addition to China, by Vietnam and India, and practically all the large multinationals with suppliers in China are doing the same,” he adds.
India is one of the most cited names. After becoming the most populous country in the world this year, ahead of China, its popularity is on the rise. It is a younger market —the average age is 28, compared to 38 in China— and it is gaining self-esteem by leaps and bounds with milestones such as its successful mission to the south pole of the Moon, or its status as host of the next G-20 summit, the forum that brings together the largest economies on the planet. Almost all analysts also agree that India has even more potential to develop. However, it has lagged behind all these years: the opening of its economy, still full of tariffs and protectionist measures, is moving slower than investors would like, and its transportation infrastructure remains deficient, as underscored last June by the railway accident in Odisha, in the east of the country, which claimed almost 300 lives and left more than 1,000 injured.
There are already voices warning that the time for India is now or never. “The China Plus One window of opportunity will not remain open for a decade. This is an opportunity [that will last] three to five years,” the new World Bank president, Ajay Banga, an American citizen of Indian descent, warned last month during a visit to a textile factory in New Delhi.
Mr. Sunjay Kapur, President, ACMA & Chairman, Sona Comstar, one of the leaders in this sector with factories in India, China, Mexico and the U.S., has closely followed the paradigm shift in global trade. “It is important to recognize that while companies will maintain their presence in China due to the colossal size of its market and the promise of continued growth, an increasing number of these companies are choosing to diversify their supply chains and expand their manufacturing operations to India, or are sourcing more from here. This change is not only boosting India’s manufacturing sector, but also catalyzing job creation and strengthening the overall economy,” he explains by email.
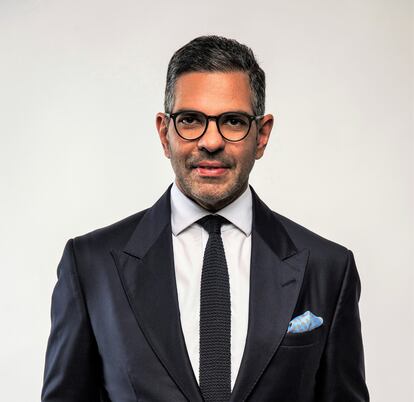
What is India’s appeal as an investment destination? Kapur highlights two: the size of the labor force and its high qualification in sectors such as information technology, engineering or the automotive industry. “This workforce provides a competitive advantage to companies looking to establish or expand their operations here.”
Apple, the most valuable company in the world by market cap, illustrates that transition. The company has a growing number of customers in India, has opened stores in New Delhi and Mumbai — with CEO Tim Cook in attendance and long lines of enthusiastic brand followers outside its doors, as often happens in the West when it releases a new model — and the volume of iPhones produced in India through its supplier Foxconn is increasing: according to Bloomberg, they already account for 7%. Some local players see an opportunity in this: the Indian conglomerate Tata has made an offer to acquire a factory in the state of Karnataka, in the south of the country, from the Taiwanese Wistron Corp, one of Apple’s suppliers, with more than 10,000 workers dedicated to assembling the iPhone 14.
Relocating raises prices
This trend is not incompatible with the indisputable dominance of China, which accounts for 75% of Foxconn’s production, according to what one of its managers recently told the Financial Times. There is not, therefore, a substitution, but a redistribution. Not just towards one country, but towards several. What consequences can these changes in supply chains have for the consumer? Cordón believes that the relocations may end up affecting people’s pockets. “The impact is going to come in the form of higher prices because the costs of supplier diversification are going to be partially passed on to the consumer.”
Logistics giants such as Maersk or the German Hapag-Lloyd, owners of two of the largest fleets of container ships on the planet, are investing in ports, warehouses and other infrastructure in other parts of Asia, taking advantage of the shower of money they received from the great global gridlock in supply chains that followed the pandemic due to the boom in demand. And among its clients are the large textile and electronics multinationals, and in general, almost anyone who moves products from Asia to the West.
Companies such as the British engineering firm IMI, the technology company Dell, and the textile giants Marc O’Polo, Mango and Dr. Martens are among those that have reduced their presence in China or have announced that they will do so in the future. In Germany, which has China as its main trading partner, and which has also been suffering the consequences of its dependency on Russian gas, the debate moves between supporters of decoupling and those who maintain a less radical view and lean towards reducing risks by diversifying markets — Volkswagen has just been ousted as the best-selling manufacturer by the local BYD, and looks to India to grow.
This trend is not helping create optimism about the Chinese economy, hit by a wave of negative data this summer due to the fall in domestic consumption and exports, the bursting of the housing bubble and the threat of deflation after prices entered negative terrain. Some analysis firms are already lowering their growth forecasts for this year. Although the foreseen growth of close to 5% is still high by Western standards, it is well below the figures of recent times, and that is a bad thing when senior managers stand in front of a map of the world and think about where to make their next move.
Sign up for our weekly newsletter to get more English-language news coverage from EL PAÍS USA Edition
Tu suscripción se está usando en otro dispositivo
¿Quieres añadir otro usuario a tu suscripción?
Si continúas leyendo en este dispositivo, no se podrá leer en el otro.
FlechaTu suscripción se está usando en otro dispositivo y solo puedes acceder a EL PAÍS desde un dispositivo a la vez.
Si quieres compartir tu cuenta, cambia tu suscripción a la modalidad Premium, así podrás añadir otro usuario. Cada uno accederá con su propia cuenta de email, lo que os permitirá personalizar vuestra experiencia en EL PAÍS.
¿Tienes una suscripción de empresa? Accede aquí para contratar más cuentas.
En el caso de no saber quién está usando tu cuenta, te recomendamos cambiar tu contraseña aquí.
Si decides continuar compartiendo tu cuenta, este mensaje se mostrará en tu dispositivo y en el de la otra persona que está usando tu cuenta de forma indefinida, afectando a tu experiencia de lectura. Puedes consultar aquí los términos y condiciones de la suscripción digital.