Global demand for batteries is depleting the supply of raw materials
Lithium-ion batteries will reign supreme for a while, but research into recycling and energy storage technologies is heating up
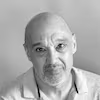

A typical home or workplace has about 10 batteries – mobile phones, watches, laptops, tablets, consoles, household appliances, tools, loudspeakers, bicycles, scooters and more. And they all use the same lithium-ion technology for power. The downside of these batteries is that they are expensive, have limited capacity and become less efficient over time. The high cost is due to the limited global reserves of their chemical elements, which are monopolized by half a dozen mining countries (China, Australia, Congo, Chile, South Africa and Indonesia). The main ingredients of these batteries are cobalt, vanadium, molybdenum, nickel, copper, graphite and manganese, among others. Increased production of electric vehicles and the need to store energy generated by intermittent renewable sources have exacerbated the problem. A study by the European Commission’s Joint Research Center (JRC) concluded that there is not simply enough raw material for so many batteries.
According to the International Monetary Fund (IMF), increasing consumption through 2050 will drive demand for battery raw materials 30-40% higher than the available reserves. CIC energiGUNE, a research center for electrochemical and thermal energy storage funded by the Basque regional government in Spain, warns, “Timely, collaborative decisions are needed.”
Zero-emission policies are also driving demand. In the next seven years, 50 million electric vehicles (EVs) are expected to hit European roads, and almost all of the 270 million vehicles expected on the roads in the EU must be electric by 2050.
EVs may be the primary driver of battery demand, but there are others. Johan Söderbom, Innoenergy’s head of smart grids and storage, said at the recent BatSum23 meeting, “Electromobility currently tops the battery market, but the demand for stationary power [from intermittent renewable energy sources, such as wind and solar] should not be underestimated.” The EU forecasts EV demand will reach 1.5 terawatt-hours (1.5 trillion watts) in two decades, and stationary batteries must produce 80-160 gigawatt-hours.
“The cost of stationary systems is much higher per kilowatt-hour of stored energy than for electric vehicle batteries because of the additional costs of the system elements,” stated the JRC report. The solution is to invest in the development of batteries such as lithium ferro-phosphate (LFP), sodium (Na-ion) and vanadium redox flow (redox-RFB) batteries.
These new battery technologies will reduce dependence on critical raw materials. More than 80% of the world’s lithium comes from Chile, Australia and China, and the Democratic Republic of Congo supplies more than 60% of the world’s cobalt. But this is not the only concern. “We need to make batteries smarter. For that, we need to improve particular aspects like cell sensors and self-repair capabilities,” said Robert Dominko, a researcher at the University of Ljubljana (Slovenia) and a member of the board of Europe’s Battery 2030+ initiative.

The JRC report notes that lithium-ion-based technologies will reign supreme in the market for the foreseeable future and details the advantages and disadvantages of the viable alternatives.
Lithium ferro-phosphate (LFP). This technology is cheaper, longer-lasting, safer and does not contain expensive cobalt and nickel. It is gaining ground in mobility and stationary applications and will become a more significant power source. However, its energy density (ratio of storage capacity to volume) is lower compared to nickel-manganese-cobalt (NMC) and nickel-cobalt-aluminum (NCA) batteries. Their major disadvantage is their low value in the recycling chain and limited manufacturing capabilities in the EU.
Nickel-manganese-cobalt (NMC). This is an expensive battery that uses less cobalt. Its main advantage is its high recycling value, but it doesn’t figure prominently in the European production chain. Batteries that use less cobalt and more nickel are widely used in the automotive industry.
Nickel, cobalt and aluminum (NCA). Tesla uses this battery extensively, which competes with LFP and NMC technologies in electric vehicle applications. It has a shorter life than NMC and less thermal stability. European production is minimal – almost zero – despite its high recycling value.
Lithium titanium oxide (LTO). These batteries have expensive elements and a low energy density. But they are safe, last longer, charge faster and are effective in high-temperature conditions. Europe currently produces LTO batteries.
Other alternatives
Sodium-ion. Johan Söderbom believes the promising sodium-ion technology will be vital to winding down lithium-ion use. According to the JRC, it’s cheaper, safer and does not use critical raw materials. However, they have a lower yield than conventional lithium-ion technologies. Much research is now focusing on sodium-sulfur batteries, which have a higher energy density and power output, longer lifespans and greater storage capacity.
Redox. Vanadium redox flow batteries mostly use vanadium dissolved in sulfuric acid, which is corrosive and toxic. “Vanadium has many positives – it’s cheap and stable. But a leak from one of these batteries is unpleasant. You have to design extremely durable containers for them,” said CIC energiGUNE researcher Eduardo Sánchez in an interview with Horizon.
The main components of redox-RFB batteries are two liquids – one positively charged and the other negatively charged. When the battery is in use, the liquids are pumped into a chamber, separated by a permeable membrane. The liquids with opposite charges exchange electrons and create an electric current. More research is underway to find chemical combinations with inexpensive, safe and non-critical materials, such as saline solutions in water that store carbon-based ions, a potential solution for seasonal energy storage.
Solid state. Traditional lithium-ion batteries have three key components: two solid electrodes (anode and cathode) and one liquid electrode (electrolyte). When the battery is in use, electrons produce power by flowing from the anode to the cathode. Positive lithium ions diffuse through the electrolyte, attracted by the negative charge of the cathode. When the battery is charging, the process is reversed. The European ASTRABAT project aims to replace this liquid electrolyte with a solid electrolyte (such as ceramic material) or a gel to achieve greater energy density, safety and manufacturing agility.
ASTRABAT coordinator Sophie Mailley says, “There is still a lack of innovation in this field… Lithium-based solid-state batteries already exist, but they use a gel as electrolyte and only work well at temperatures around 60°C [140°F], which isn’t suitable for many applications.”
Other batteries in development include the lithium-ion batteries with silicon-rich anodes that Mercedes-Benz will start using in 2025, the lithium-metal batteries that Volkswagen is betting on, and the lithium-sulfur or lithium-air batteries that use lithium oxidation at the anode and oxygen reduction at the cathode to generate electricity.
All these R&D efforts are based on the conviction that the best known, cheapest and most mature batteries used today for starting combustion vehicles or as auxiliary systems “cannot maintain their market leadership position with electric mobility on the rise,” according to the JCR report.
Recycling
Another critical aspect of ensuring the future availability of batteries is recycling, which could reduce lithium, cobalt and nickel extraction by 25-35% in 15 years, according to a report by the Institute for Sustainable Futures at the University of Technology Sydney (Australia). Worldwide, 600,000 metric tons of lithium-ion batteries are currently recycled, which is expected to exceed 1.6 million metric tons by 2030.
But recycling batteries and their metals is difficult and expensive. “An electric vehicle battery is a very complex piece of technology with a lot of different components in it – so a recycling facility is going to be very complicated. In the long run, that’s going to be important, but in the short run, it has a ways to go,” said Michael McKibben, a geologist at the University of California, in an interview with Knowable.
According to a study published in ScienceDirect, the cost of recycling lithium from batteries is five times higher than lithium extracted from mines. Moreover, some recycling processes, such as smelting the devices for metal extraction, consume a lot of energy, emit toxic gases and fail to recover the coveted lithium. Research into more efficient processes is underway.
Sign up for our weekly newsletter to get more English-language news coverage from EL PAÍS USA Edition
Tu suscripción se está usando en otro dispositivo
¿Quieres añadir otro usuario a tu suscripción?
Si continúas leyendo en este dispositivo, no se podrá leer en el otro.
FlechaTu suscripción se está usando en otro dispositivo y solo puedes acceder a EL PAÍS desde un dispositivo a la vez.
Si quieres compartir tu cuenta, cambia tu suscripción a la modalidad Premium, así podrás añadir otro usuario. Cada uno accederá con su propia cuenta de email, lo que os permitirá personalizar vuestra experiencia en EL PAÍS.
¿Tienes una suscripción de empresa? Accede aquí para contratar más cuentas.
En el caso de no saber quién está usando tu cuenta, te recomendamos cambiar tu contraseña aquí.
Si decides continuar compartiendo tu cuenta, este mensaje se mostrará en tu dispositivo y en el de la otra persona que está usando tu cuenta de forma indefinida, afectando a tu experiencia de lectura. Puedes consultar aquí los términos y condiciones de la suscripción digital.