The world urgently looks for alternatives to lithium batteries
The shortage of materials for common storage systems accelerates research into sodium and calcium as cheaper and more ecological substitutes
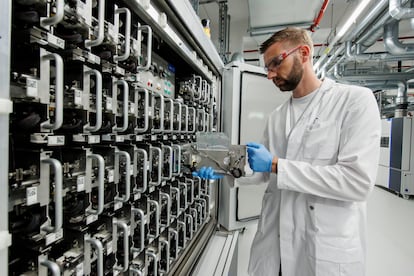
The use of elements such as lithium, cobalt and nickel for the production of batteries implies a dependence on scarce (and, therefore, expensive), toxic materials whose extraction and processing causes numerous environmental problems. Two million liters of water are needed to extract 1,000 kilos of lithium. Researchers are urgently searching for substitutes that are abundant, renewable, biodegradable, safe, low-cost and with little environmental impact. The solution may be near: sodium and calcium, two abundant elements that are being investigated to prevent lithium demand from multiplying by 60 in two decades, according to European Union forecasts.
Added to the unstoppable proliferation of home and portable devices are the two biggest challenges facing society: the electrification of mobility and the storage of renewable energy to provide continuous power. “There are not enough lithium, cobalt and nickel ions to satisfy everyone’s needs,” says John Abou-Rjeily, a researcher at the company Tiamat Energy, which emerged from the French National Center for Scientific Research (CNRS ) and which designs and manufactures sodium-ion batteries.
As reported in the UE’s Horizon magazine, this doctor in Physics and Chemistry of Materials is investigating the possibilities of sodium, one of the most abundant chemical elements in the Earth’s crust, and which is safer and cheaper to process than lithium. On the downside, it requires more space, which is why current batteries are not yet suitable for very small devices.
They also cannot compete with the range that current storage systems bring to electric cars, but they could serve as alternatives on shorter routes, which account for the majority of car trips. “While I would never challenge the 500-kilometer range of lithium-ion batteries, this type of sodium-ion could be more competitive for short and medium distances by car, explains Abou-Rjeily.
Researchers from the Chalmers University of Technology (Sweden) and Delaware University (United States) are working along the same lines, according to a study published in Energy. “There is a tendency to demand a really large battery. But according to research, generally, a slightly smaller one, with less range than that of a gasoline tank, is sufficient, since the only time in which you would need a greater autonomy is for a trip of six hours or more, in which case, the driver could charge on the go. There is too much emphasis on the need for a really long range and this leads to an increase in the price of the vehicle and a greater use of resources for electric cars,” says Frances Sprei, a professor at Chalmers.
For this doctor in Energy and Environment, this change in mentality is necessary to adapt charging facilities where people spend the most time: at home and at work. Sprei regrets that, on the contrary, many European countries focus on the charging network on roads.
This simple modification of the perception of needs would further promote sodium as an alternative, since it would allow the technology to be deployed in homes and workplaces as energy storage systems from renewable sources. This is the goal pursued by Magdalena Graczyk-Zajac, a visiting professor at the Technical University Darmstadt in Germany, and member of the European SIMBA project, a EU-funded initiative to develop a sodium-ion battery for homes which concludes its first phase next June.
You could be driving your car for free for eight to nine months of the yearMagdalena Graczyk-Zajac, profesora de la Universidad Técnica de Darmstadt
This researcher is committed to finding ways to store the energy captured by home photovoltaic panels in a rechargeable sodium ion domestic battery. This would power the homes and charge the electric vehicles of its residents with a significant cost reduction. “You could be driving your car for free for eight to nine months of the year,” she says. A prototype is already in laboratory tests.
One part of the battery, the anode, is made from hard carbon, which can be manufactured from wood or biowaste. Another, the cathode, can be made of a material called Prussian white, a chemical compound from a blue pigment of the same name, but with more sodium and rich in iron, one of the most abundant metals.
The Basque research center CIC energiGUNE has its own development in this area: a sodium metal anode with a thickness of only seven microns (70 times thinner than the current ones) achieved through a physical evaporation process. According to this center, the advance opens the door to the manufacture of flexible solid-state batteries with the thin sodium anode, a safer, cheaper and smaller alternative to the current batteries with liquid electrolyte in which graphite is used.
“Sodium cannot be easily laminated due to its sticky texture, similar to plasticine,” explains Montse Galcerán, the principal researcher of this project. “To date, the most common method used to roll a block of sodium was as basic as processing it with a hammer, but this meant that a thin and homogeneous sheet could not be obtained, and, therefore, there was a large excess of unused sodium in the batteries. Thanks to evaporation, we have managed to overcome that obstacle,” she says.
This thinning of the anode allows researchers to reduce the amount of sodium needed, as well as the costs, weight and dimensions of the batteries, while increasing energy density (greater storage capacity) and safety.
If the raw material is cheap, so can the batteriesRosa Palacín, Institute of Materials Science of Barcelona (ICMAB-CSIC)
Another element that is used as a substitute for lithium is calcium. “It is one of the most abundant elements in the Earth’s crust and it is not concentrated in specific geographic areas, as is the case with lithium. If the raw material is cheap, the batteries can also be cheap,” says Rosa Palacín, from the Institute of Materials Science of Barcelona (ICMAB-CSIC) and a member of the CARBAT project.
Using calcium as a negative electrode offers advantages over graphite in lithium-ion batteries, since it has a greater accumulation capacity per kilogram (energy density) than conventional lithium batteries, which also form tiny rigid structures called dendrites and can cause short circuits or explode after many uses, according to this institution.
“When calcium passes through the electrolyte, two electrons flow out, instead of one, as in the case of lithium. It can be assumed that a battery of the same size would offer greater autonomy if used in an electric vehicle, as long as a suitable positive electrode is found,” explains Palacín.
The key is choosing the most appropriate components. “It appears that ultimately all working electrolyte salts contain boron. We use calcium tetrafluoroborate dissolved in a mixture of ethylene and propylene carbonate,” says the researcher.
Other researchers from the Technical University of Denmark are searching, as part of the SALBAGE project, for a battery made from an aluminum anode and a sulfur cathode. Aluminum is even more abundant than calcium, but incorporating it into a battery poses similar difficulties.
“All the materials used are cheap. Aluminum, sulfur, the electrolyte itself and urea are very, very cheap. Even the polymer is,” says the researcher Juan Lastra, who defends this option to store energy from a wind or solar park.
Sign up for our weekly newsletter to get more English-language news coverage from EL PAÍS USA Edition